AKT OIL SERVICES industry is always in the frontline seeking to improve their production capacities, minimize machinery downtime and optimize the overall process efficiency.
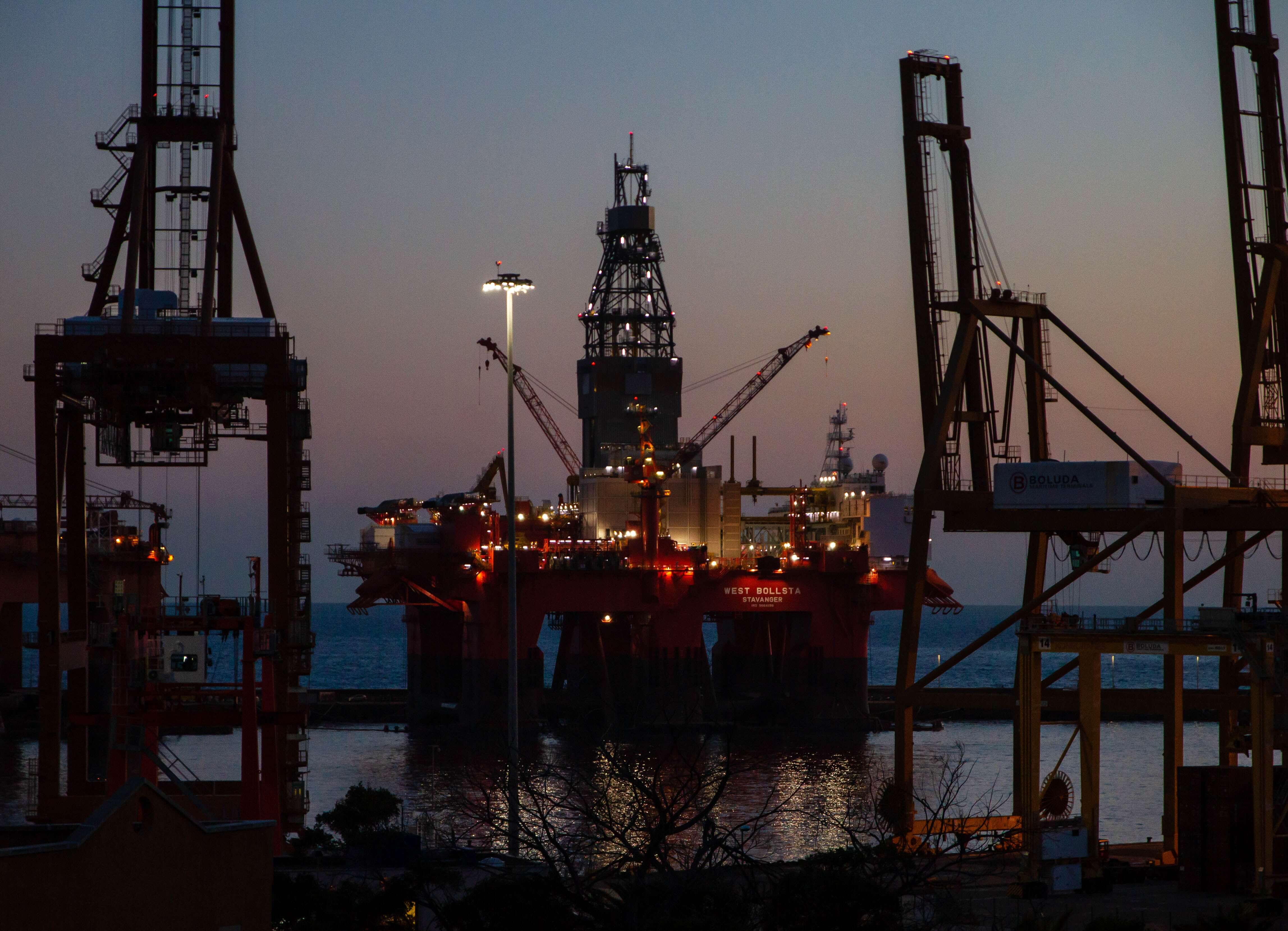
Among other services, AKT OIL SERVICES has employed chemical injection packages to not only increase production but also improve separation of oil/water/gas, reduce corrosion and generally improve the profitability of all the exploration and recovery efforts. Wellhead chemical Injection is a process that involves the introduction of specialized chemicals to the oil and gas flow stream or reservoir to perform certain specific processes. In other words, a secondary chemical solution is normally added to the primary process flow to improve the primary fluid’s quality or to enhance the flow of primary fluid. These specialized chemicals can be injected into the produced oil and gas flow stream from the wellhead or can be injected through an annulus down hole into the oil and gas reservoirs. This process helps in the improvement in the production capacity, efficiency and reduction in the downtime.
The benefits of chemical injection are numerous. These benefits have not only made it a necessary factor in the oil and gas industries but has also become a solid investment, while on the other hand promoting an environmentally friendly work atmosphere. Among others, these advantages include:
- It helps in the prevention of corrosion from the wellhead and all the way to the refinery. It decreases the drag and friction inside the pipes along with the decreases machinery down time, maintenance, repairs etc and thus in effect a better and increased production flow.
- The safe and sound deployment of chemical injection process in a hazardous prone environment through the use of safety shutdown valves and control instrumentation provides eminent safety while preventing both machinery and personnel from harm’s way.
- Its easy process of installation and maintenance has greatly reduced maintenance costs, repairs and downtime. This element has made this technology extremely cost-effective process as it allows the continuation of production with less difficulties.
- The chemical injection systems are normally skid-mounted thus helps it to be portable. These steel skids provide it with the required structural integrity during routine operations and allows for the safe operation and transportation.
- Chemical injection has different purposes which may deploy different processes hence the factor of flexibility in the scale is an advantage. Besides, the use of the chemical injection packages with specialized designed packages makes it effective and versatile.
The main components of a wellhead Chemical Injection System in Oil and Gas
A fully functional chemical injection system comprises of various components that are assembled on a skid so as to enhance portability as well as operational functions. This in overall results in the optimization of productivity in the industry. Although a number of variations may occur depending on end-user preference, the components described below are commonly present in one form or the other.
Metering pumps- Every chemical injection system requires metering pumps whose general purpose are to convey the chemicals into the targeted oil formations. They pump the chemical into the flow stream or the reservoir with precisely the accurate amount of chemicals and with the required back pressure. Injection pumps sustain a steady flow of chemical solution throughout a wide range of pressures for optimized performance. It may be a continuous process or an intermittent process depending on the requirements of that package. Chemical injection pumps can comprise of a plunger, diaphragm or double diaphragm configurations which are powered by electric motors, pneumatic systems or solar energy. In addition, solar energy has already made the whole system to be self-sustaining as the power source. Research shows that the latest advancements and the engineering body are solely focused on improving the performance of the chemical injection packages by minimizing the system size while maximizing the overall performance thus deriving much better efficiency from the system. The reduced size will make it well suited for space constrained locations while reducing maintenance time and costs.
Chemical injection storage tanks- Storage tanks are vessels that are indispensable to the chemical injection process in any oil and gas industry. These vessels store the vital chemical solutions to be injected into the system so as to enhance separation, improve oil recovery, decrease foaming and impede channel corrosion. These tanks are normally custom-built to suit our end-user specifications, preferences and space considerations. The tank structures are available in a wide range of shapes from cylindrical, rectangular or square form.
Instrumentation and control panels- these are the core of the chemical injection system as they are vital for monitoring critical system parameters. A typical instrumentation measures pump flo rate, suction tank level, pump discharge pressure, pulsations and also temperature. Multiple injection points in the system can be managed by the use of a metering pump and special devices known as multiple injection rate control devices (IRCD) which separately meter the injection chemicals to the individual injection points.
Skid-mounted instruments- They primarily monitor and record logs of the operating conditions within an injection point in a system. These units also help to predict and prevent adverse situations by performing automatic shutdowns. Apart from automated fail-safes, chemical injection systems may also possess inbuilt alarms and manual shutdown valves.
Suction and discharge piping & valves- the main role of the suction piping and manual valves in the system is to transfer the vital chemical from the chemical injection storage tanks to the metering pump. On the other hand, the discharge piping and manual valves transfer the high-pressure chemical from the metering pump to the skid edge, where the chemicals are routed to their final injection location. The various components such as gate valves, ball valves, check valves, calibration columns collectively form the overall chemical injection system.
Skid compatibility- Most chemical injection systems are skid-mounted. Compatibility with a steel skid mount allows safe transport and operation while providing structural protection to the system during routine operations. Process skid manufactures like AKT OIL SERVICES have several solutions for your chemical dosing and injection needs.
Despite the various benefits that come along with wellhead chemical injection, one of the most common challenges during the operational phase is the drainage challenge. A common misconception is that if the surface end of the injection line is not open ended, then injection line drainage cannot occur. That is not true at all. The surface end of the injection line could be closed, but the injection chemicals is likely to drain from the line if pressure in the injection line vary. This is attributed to the fact that the hydrostatic pressure head of the injection chemical and any pump discharge pressure is greater than the pressure in the tubing. Simultaneously, the injection chemical at the surface end of the line may vaporize and the liquid vapor interface falls within the injection line, until the pressures across the down hole injection valve equalize. This problem is quite expensive because it not only results into cost overruns of chemicals but there is also a possibility that there will be disruption in the treatment regime, this vaporization of the injection chemical often results into a change of the physical properties within the remaining liquid phase. This in turn can result in crystallization and gun king or subsequent line blockage, rendering the chemical injection system useless.
However, the AKT OIL SERVICES has devised a method to successfully combat this challenge by developing modern modular valves which integrate two check valves in series. The downstream valve also incorporates the same check valve module successfully. These check valves were designed using computational fluid dynamics, to ensure that the valve flow paths as well as the opening dimensions were optimized with regard to erosion by minimizing the flow velocity across and the flow stream angle of incidence with respect to the metal/metal seal faces. Moreover, in order to successfully eliminate the potential for injection line drainage, an additional valve is incorporated in series immediately upstream of the check valve. This upstream valve uses the same working principles as the check valve but is held closely by a much stronger spring.
In conclusion, wellhead chemical injection packages have been a prime factor in the improvement of profitability through the several ways discussed above. It inhibits freezing in the production line, enables separation crude oil/water/gas, enables removal of the deposits of salt, wax and other minerals build up which results in reduction in the production, prevents corrosion and most importantly, can be monitored and controlled through the instrumentation panel and diagnostic software to monitor the performance. All these wonderful benefits combined together give the chemical injection system a great value and becomes indispensable. Therefore, chemical injection packages are truly a great benefactor for the oil and gas industry in its growth.
At the AKT OIL SERVICES, we are dedicated to providing our clients with the most efficient, first class, modern modular wellhead chemical injection packages. For project operators out there looking to gain a competitive edge in the oil and gas industry, AKT OIL SERVICES is the right fit for you.
AKT's editorial partners have cut their teeth at The New York Times, Wall Street Journal, Time, Inc., and Bloomberg.